With the current state of the supply chain, there are many obvious reasons to become a Shipper of Choice, with the biggest reason simply keeping your product on the shelves and in front of consumers. While respect for drivers and carriers is a big part of the equation and goes a long way to achieving the designation, there are several optimizations where technology can speed up time on site for the driver and bring numerous operational benefits to any facility.
While no official designation exists, the best way to define Shipper of Choice is a shipper that carriers want to work with. As with every business, time is money, so the more time-efficient shippers are, the more cost-efficient both shippers and carriers can be.
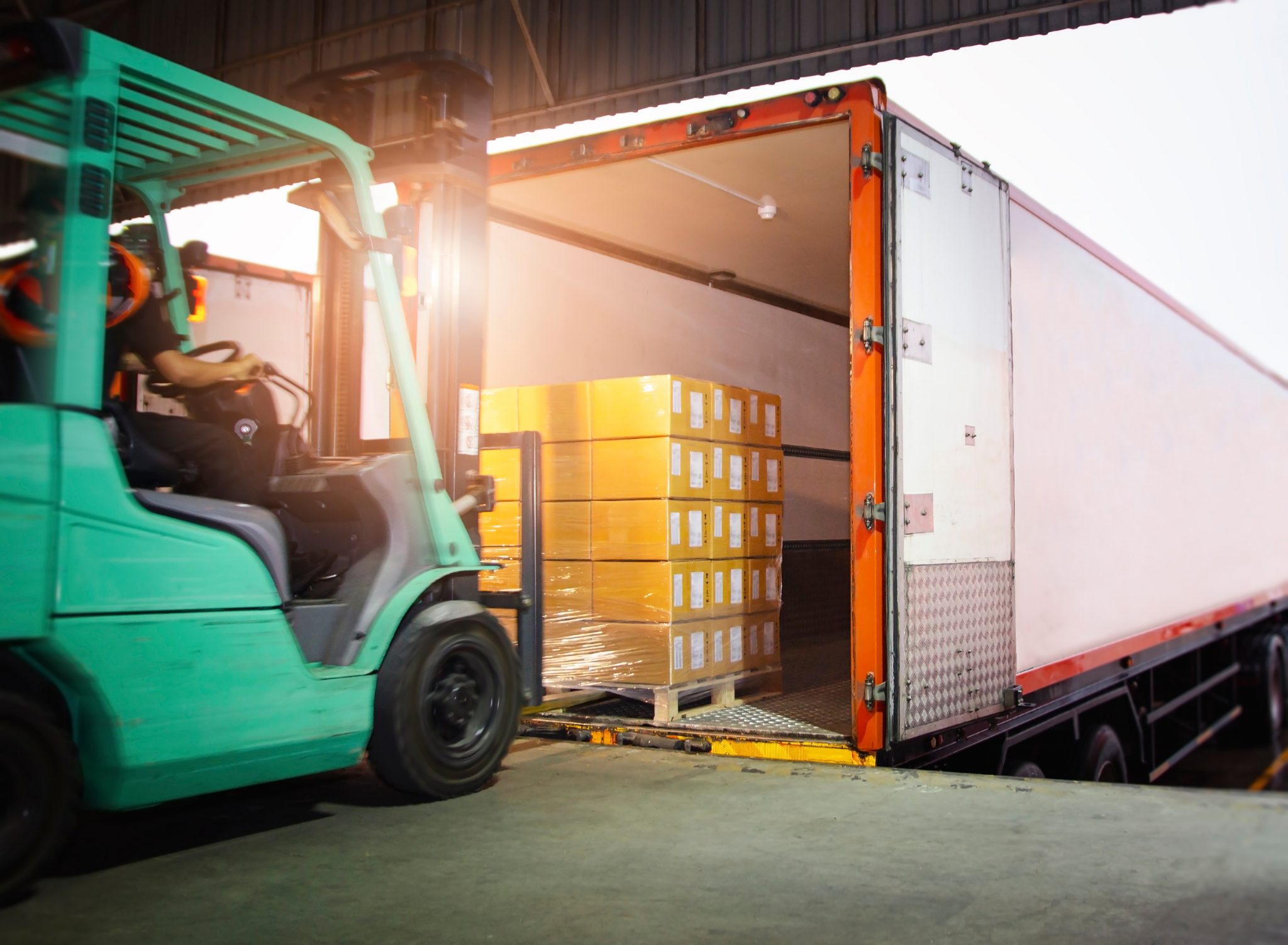
So how do you speed up the process at your facility, remove inefficiencies, and make moving goods easier for all involved?
- Kill the queue. – There’s nothing more frustrating than wasting time waiting in line before a driver even gets into the facility. It’s a sign of a facility run without adapting to current demands. Going guardless at the gate with automated ingress/egress or remote gate monitoring will speed up the first and last steps in the process.
- Communicate with drivers. – Providing clear instructions to a driver on where to go within the facility and where to drop or pick up a trailer eliminates confusion in the yard and can most effectively be done via SMS text or other automated communication tools.
- More lead time and more flexibility. – Late notice makes it difficult for carriers to plan their schedule effectively and no one likes to scramble. Provide at least 48 hours lead time along with open appointment times and extended hours/weekends to increase the likelihood of providers accepting your loads.
- Go paperless. – Going digital and removing paper from the entire workflow creates efficiencies throughout the process. Digital signature capture saves time with signing once versus multiple times and creates a timestamp for data tracking. With digital document management and cloud storage, carriers can receive shipping documents immediately, customer service inquiries are faster, lost bills of lading are a thing of the past, and any shipping document can be found in a few seconds instead of a venture into the warehouse and a shelf full of Banker’s Boxes. Paperless is also greener and more sustainable.
- Improve dock door efficiency. – Properly coordinating staging, selecting the optimal dock door, and improving load times all combine to eliminate excess dwell time and poor trailer utilization.
- Use data to inform decisions. – Real-time dashboards tracking relevant KPIs provide the data needed to make quick decisions and improve the process over time.
- Communicate with carriers. – Building relationships with carriers and providing transparency will pay dividends for both sides down the road. If a relationship exists, a carrier is more likely to prioritize those loads. Responding to issues as they arise is also key. But the simplest thing you can do is have a conversation with your carriers. “What can we do better?” is a great place to start for shippers.
- Pay promptly. – While a fairly obvious suggestion, paying invoices and any added fees quickly and accurately helps demonstrate you value and respect the carrier. Who would you rather do business with – a business paying invoices upon receipt or 75 days later?
By focusing on the turning trailers with speed and efficiency and building the shipper-carrier relationship with respect, transparency, and trust, an organization earns Shipper of Choice status and creates cost-efficiencies for both partners.
What does your organization do to earn sustained business from carriers and be a Shipper of Choice? Email your recommendations to editor@warehouserevolution.com.